How to Add Shopify to WordPress with ShopWP
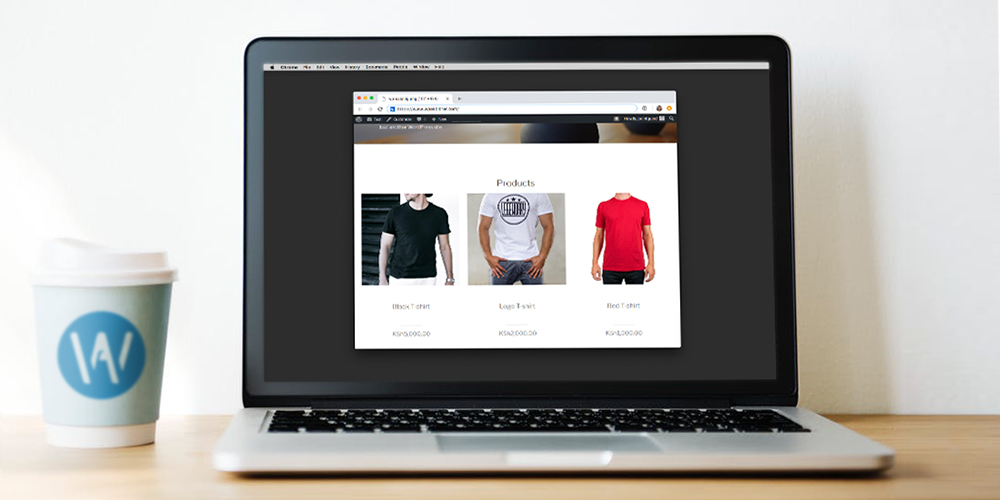
Shopify is arguably one of the best e-commerce platforms of our time. WordPress, on the other hand, is the best content management system on the web. Link the formidable e-commerce functionality of Shopify with the powerful CMS features of WordPress via the ShopWP plugin, and you get all the tools you need to build an online store that’s out of this world.
Or, wouldn’t it be awesome to sell your Shopify products on WordPress? In this review slash guide, we show you exactly how to setup the ShopWP plugin so you can tap into the power of WordPress and Shopify like a boss.
The ShopWP plugin helps you extend your Shopify store using native WordPress functionality. For example, the plugin allows you to take advantage of the wide range of WordPress themes and plugins to enhance your store. For a clearer picture, you can think of WordPress as the e-commerce front-end and Shopify the back-end.
With that preamble, let us discover why ShopWP is the best way of integrating WordPress with Shopify. Sounds awesome, right? Great, let’s dance.
What is ShopWP?
ShopWP is a nifty plugin that allows you to sell Shopify products on your WordPress site without installing and configuring an e-commerce system such as WooCommerce.
The plugin syncs your Shopify store data as custom post types offering you the opportunity to use the full power of the WordPress CMS. Further, ShopWP helps you to add the Shopify Buy Button anywhere on your WordPress site, making for a seamless buying experience.
ShopWP doesn’t handle payments. Once the buyer hits the checkout button, they are redirected to your Shopify checkout page to complete the transaction. In other words, you will only use Shopify to process payments.
If you’ve used Shopify before, you know it’s a powerful e-commerce platform, but it has nothing on WordPress as a website builder.
Notable ShopWP Features Include:
- Ability to import your Shopify products and collections as WordPress posts
- Countless templates that help you to build an online store out of this world
- Use the Shopify SDK to host a fully-featured shopping cart on your WordPress store
- No iFrames thanks to the responsive Shopify Buy button
- SEO-ready design
- Capability to save your Shopify store data in custom WordPress database tables
- 100+ actions and filters that help you to customize your online store whichever way you desire
- Compatibility with WordPress themes and plugins
ShopWP Pro also includes access to 80+ templates, auto and selective syncing with your Shopify store, cross-domain tracking, dedicated support and more.
What Are The Benefits of Using ShopWP?
Features aside, ShopWP allows you to enjoy some benefits you would miss if you sold on Shopify exclusively. Here is a tiny list to whet your appetite.
- You have full control over the URL structure of your products thanks to WordPress permalinks
- Access to thousands of WordPress themes and visual page builders, which means you can build the store of your dreams without breaking a sweat
- Customizing WordPress themes is easier than using Shopify’s Liquid template engine
- Unlimited access to thousands of WordPress plugins allowing you to add rich functionality to your store
- Unlike Shopify, you have total control of the store data you sync with WordPress
- You can take full advantage of Shopify’s inventory and order fulfillment features, while riding on the back of WordPress
- Discounted shipping rates
- ShopWP is easy to install and configure as you’ll learn in a moment
- Extensive documentation and FAQ
- Great support
How to Setup ShopWP
In this section, we learn how to setup ShopWP and integrate it with Shopify. Some of the instructions below may be a bit off since the free version of ShopWP has been retired.
That out of the way, let us get to work.
Installing ShopWP
Seeing as ShopWP is available on the official WordPress plugin repo, you can install it directly from your WordPress admin dashboard.
How? Navigate to Plugins > Add New.
On the Add Plugins page, use the Upload button to install ShopWP.
Activating the plugin adds a ShopWP sub-menu on your WordPress admin menu. Navigate to ShopWP > Settings to start the integration with your Shopify store.
At this juncture, we are assuming you already have a Shopify store (even if it’s the free 14-day trial). We created a free trial account for this guide, and added a couple of products. Here’s how our Shopify catalog page looks like.
Not so fancy, but it should work perfectly.
Moving on, clicking on the Settings sub-menu takes you to the Connect tab shown below.
From the screenshot shown above, you need a couple of details, which you’ll obtain from your Shopify admin area. These details are:
- API key
- API password
- Shared secret
- Storefront access token
- Domain (this is your Shopify store domain e.g. wpex.myshopify.com we used for this guide)
Generating ShopWP Integration Details
Login to your Shopify store admin dashboard and click Apps as shown below.
This will lead you to the Apps screen. Click on the Manage private apps link as we highlight below.
Next, click the Create a new private app button as we outline below.
On the next screen, enter your private app name and email address. Next, under the Admin API section, set everything to Read and Write. Set the permissions to Read Access for any field that doesn’t have the Read and Write option.
After that, tick the Allow this app to access your storefront data using the Storefront API checkbox towards the bottom of the page as shown below.
Finally, hit the Save button and the subsequent I understand, Create the App button. Once done, Shopify will present a page with your API key and all the other details you need to integrate the ShopWP plugin. See image below.
Note: You can find your Storefront access token towards the bottom of the same page as shown below.
Now, just copy-paste the details into the respective fields on the ShopWP Connect tab as we detail below.
Next, hit the Connect your Shopify store button shown in the image above to initiate sync.
And that’s it, your Shopify shop is now synced with your WordPress site. Successful syncing will show the Connected status as shown below.
Now, if you navigate to ShopWP > Products on your WordPress admin menu, you’ll see that the ShopWP plugin has imported all of your products from Shopify.
Products shown in the image above were imported directly from our Shopify demo store. You can import up to 250 products at once.
And here is how the catalog we just imported looks on our WordPress demo site using the Twenty Seventeen theme.
Let us now explore the other features available within the ShopWP admin dashboard. So here we go!
Settings Tab
The Settings tab offers you plenty of options to manage your online store with ease. From here you’ll find settings to control:
- Product URLs
- The number of products per page
- Syncing
- Breadcrumbs
- Pagination
- Product display layout including images, colors,
- Collection display layout
- Related products
- Cart
- Checkout process
- And so much more
Tools Tab
The Tools tab helps you to resync Shopify data, clear ShopWP Cache and Remove all synced data from WordPress.
License Tab
The License tab comes in handy if you are looking to upgrade to the pro version of ShopWP. Which if you didn’t know offers you even more features to super-charge your Shopify-WordPress hybrid store.
Debug Tab
And the Debug tab allows you to spot errors and get support.
Misc Tab
At the time of writing, the Misc tab allows you to upgrade database tables if you upgraded from a version below 1.2.2.
Conclusion
While you can use the Shopify Buy Button, ShopWP is probably the best plugin to sell your Shopify products on WordPress. The plugin is carefully designed and ships with all the tools you need to start selling right away. Additionally, it’s super-duper easy to setup, you should be done in less than 10 minutes.
What’s your opinion regarding ShopWP? Please share your questions and thoughts in the comment section below.
How do I put all the products on one page? Or add products to collections?
All of your products and collections should be automatically added to WordPress as posts. So once imported, ass of your products should be visible on yoururl/products and collections at yoururl/collections. You can also use the included plugin shortcodes for [wps_products] and [wps_collections] to add your products or collections to any page. Hope that helps!
Sadly this plugin never worked for my site and the developer was very very involved in trying to help me get it to work.
Really wished it had. We’re not sure if it’s because I’m on dreamhost or not. But in case it is, if you’re on Dreamhost and notice it’s not working, that may be why.
That’s a bummer! I hope you were able to get Shopify working on your site manually.
That said, I do know that Dreamhost’s shared plans can be pretty limited – many don’t offer enough resources for most premium themes or plugins to even function. If you’re on a shared plan with them consider upgrading to their managed hosting which I know does in fact work so much better than their standard shared plan. And if you’re already on a managed plan reach-out to their support team – sometimes a setting just needs to be tweaked to get things working.
We alrady tried a lot of different modules to implement Shopify with WordPress together but your solution looks pretty fine! We’re just launching our new Crypto merchandise shop with Bitcoin Shirts and more and we want to have some other satellite pages where we just can add your solution into a small wordpress page which has access to our main shopify crypto store. We change from dreamshost shared plans which are limited as you say to another hosting. Thank you for your blog buide with that amazing wordpress shopify plugin.
Hey, I am using this app and so far really like it, it does everything my client needs. Just having trouble finding the templates to customise the design, they are nowhere to be found… Can anyone point me in the right direction please. I’d be ever so grateful. Thank you so much.
The WP Shopify templates are a part of the pro version – so first you’ll need to make sure that you have a paid plan, then you can use the documentation to locate and edit templates.